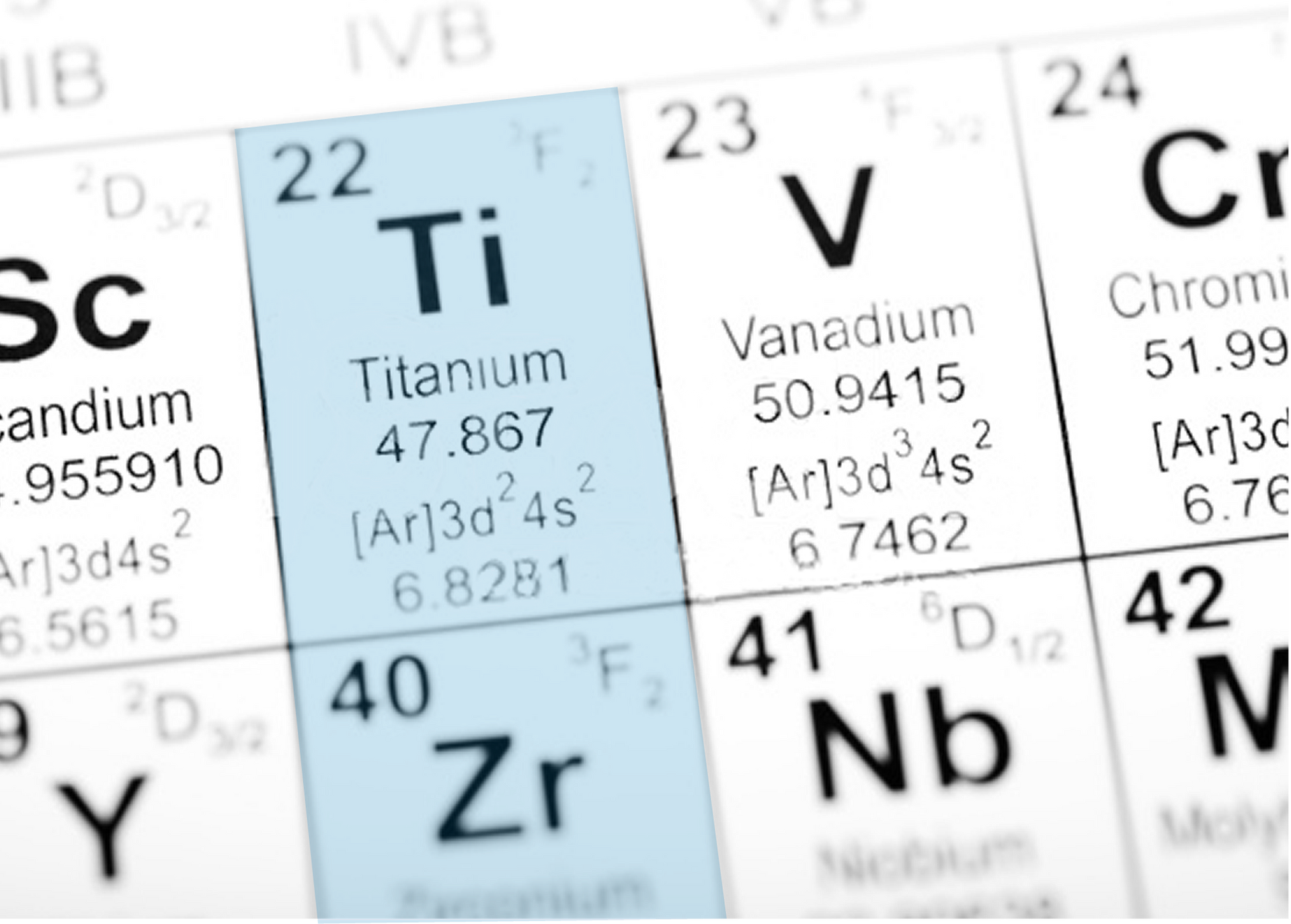

Coatings and Repairing For MRO
Why ZTP-DeD Powder Is Unique
The vision of Z3DLAB is not limited only to L-PBF technology which was used to process ZTP10 powder.Actually, because of the MRO market that continues to grow , we developed this powder so it could fit the Cladding and DED technologies. That is why ZTP-DeD was developed and it is specifically designed for MRO market. The First Application of ZTP-DeD was the design and the making of a normalized shackle used to hold a F35 air fighter to the ground. Initially they were made by Ti64. But due to the high erosion and solicitation, the life of these Ti64 made schale is very low, That is why ZTP-DeD was used to increase the life-span of these schacle form more that 35%.


Why ZTP-DeD From Z3DLAB
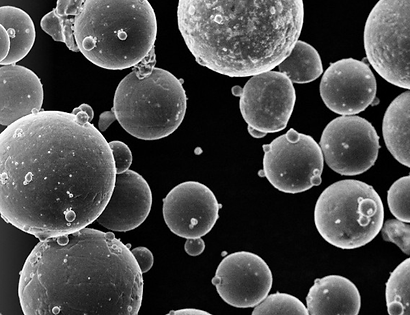
Makes Parts Was Never Easy – Already well developed DED process, thanks an Eureka Labeled Program.
​
Lighter Than Steel and CoCr – Thanks to the improved ratio of Density To Mechanical Resistance, parts are designed and produced to be 50% lighter.
​
Makes High Value Parts – Due to the enhanced process of DED, fewer imperfections in the printing , parts made with ZTP-DeD powder consistently and reliably outperform other AM parts.
​
Makes AM predictable – Due to the monitoring system equipped to develop the process parameters of ZTP-DeD, now it is easy to pecit and reproduce parts with an easy mind.
Revive or Give New Life To Your Medical Parts
Aerospace and Medical field maybe two different fields but they share a material in comment which Ti64. However, this material is used for generations without knowing any upgrades.
​
Very Strong Layer Adhesion – With ZTP-DeD, it is possible to coat the already existing Ti64 parts. The result is an increase in adhesion strength of the deposited layer in contrary to other alloys.
​
Build Parts From Scratch – In some applications, coating is not recommended. New parts could be printed using ZTP-DeD powder.
​


